Exploring the Advantages of 3D Printing for Toy Manufacturing
3D printing has revolutionized various industries, including toy manufacturing. This innovative technology offers numerous advantages that traditional manufacturing methods cannot match. Let’s delve into the benefits of using 3D printing for toy production.
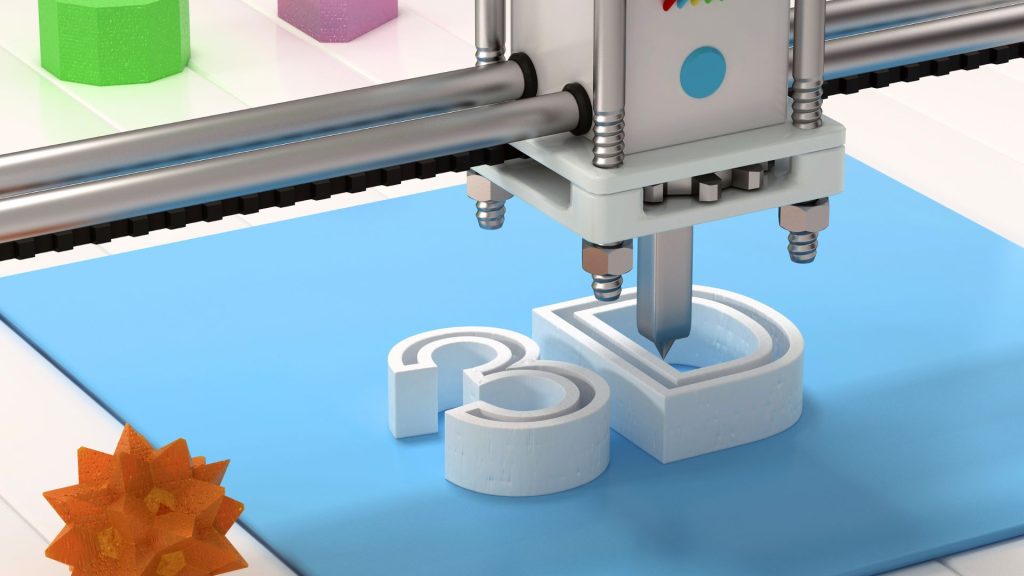
1. Design Flexibility:
One of the most significant advantages of 3D printing is its unparalleled design flexibility. Unlike traditional manufacturing techniques, which often have limitations in terms of complexity and customization, 3D printing allows for the creation of intricate and highly detailed toy designs. Toy manufacturers can easily customize designs to meet specific requirements or incorporate unique features, resulting in more diverse and engaging toy offerings.
2. Rapid Prototyping:
Another key benefit of 3D printing is rapid prototyping. Traditional prototyping methods can be time-consuming and costly, requiring the creation of molds or tooling. In contrast, 3D printing enables rapid iteration and testing of toy designs with minimal setup time. Manufacturers can quickly produce prototypes, evaluate them for functionality and aesthetics, and make necessary adjustments before moving to full-scale production. This iterative process accelerates the product development cycle, allowing for faster time-to-market and greater agility in responding to consumer demands.
3. Cost-Effectiveness:
While initial investments in 3D printing technology and materials may seem daunting, the long-term cost-effectiveness of this manufacturing method is undeniable. 3D printing eliminates the need for expensive molds or tooling, reducing upfront costs associated with traditional manufacturing. Additionally, 3D printing enables on-demand production, minimizing inventory costs and waste by producing toys only as needed. Over time, these cost savings can significantly impact the bottom line, making 3D printing a financially attractive option for toy manufacturers.
4. Customization and Personalization:
In today’s consumer-driven market, customization and personalization have become increasingly important factors in purchasing decisions. 3D printing excels in this regard, allowing for easy customization of toy designs to meet individual preferences or market trends. Whether it’s adding a child’s name to a toy or creating unique variations of a popular character, 3D printing enables manufacturers to offer personalized products that resonate with consumers on a deeper level.
Overcoming Challenges in 3D Printing for Toy Manufacturing:
While 3D printing offers numerous advantages for toy manufacturing, it also presents unique challenges that manufacturers must address to maximize its potential. Let’s explore some common challenges associated with 3D printing for toy production and how manufacturers, such as Bidso, can overcome them:
1. Material Selection:
Choosing the right materials for 3D printing toys is crucial for achieving the desired quality, durability, and safety standards. Bidso conducts thorough research and testing to select materials that meet regulatory requirements and consumer expectations. By partnering with reputable material suppliers and staying informed about the latest advancements in 3D printing materials, Bidso ensures that its printed toys are safe, reliable, and of high quality.
2. Print Quality and Consistency:
Achieving consistent print quality is paramount in toy manufacturing, especially when producing complex or intricate designs. Bidso invests in high-quality 3D printers and employs skilled technicians to fine-tune printing parameters and monitor the printing process. Through rigorous quality control measures, Bidso maintains consistency across production batches, minimizing defects and ensuring that its printed toys meet the highest standards of quality and craftsmanship.
3. Post-Processing and Finishing:
While 3D printing offers unparalleled design freedom, printed toys often require post-processing and finishing to achieve the desired aesthetic and functional properties. Bidso has developed efficient post-processing workflows and techniques to streamline production. By investing in advanced finishing equipment and training its staff in the latest post-processing techniques, Bidso ensures that its finished toys are visually appealing, safe, and ready for market.
4. Scalability and Production Volume:
Scaling up production with 3D printing can be challenging due to limitations in print speed, build volume, and material availability. Bidso carefully assesses production requirements and optimizes printing processes to achieve the desired scalability and production volume. By leveraging hybrid manufacturing approaches and exploring new technologies, Bidso maximizes the efficiency of its 3D printing operations, allowing it to meet the demands of its customers and the market.
Conclusion:
Despite its challenges, 3D printing offers tremendous potential for innovation and growth in the toy manufacturing industry. By addressing challenges related to material selection, print quality, post-processing, and scalability, manufacturers like Bidso can unlock the full benefits of 3D printing and drive meaningful change in the industry. With a commitment to quality, innovation, and continuous improvement, Bidso is at the forefront of leveraging 3D printing technology to create safe, durable, and engaging toys for children around the world.